-
Eintrag vom 24.07.2025
Condition Monitoring auf der HUSUM WIND 2025
-
Eintrag vom 16.07.2025
Condition Monitoring spart Anlagenbetreibern viel Geld
-
Eintrag vom 27.03.2025
Condition Monitoring Seminare - Rechtzeitiges Erkennen von Getriebeschäden
-
Eintrag vom 27.01.2025
Tonnenkupplungsüberwachung - Automatisches Condition Monitoring an Kranen
-
Eintrag vom 18.10.2024
Condition Monitoring und Künstliche Intelligenz
-
HUSUM WIND 2025
16.09.2025 - 19.09.2025
-
Grundlagenseminar Condition Monitoring
07.10.2025 - 08.10.2025
-
Produktschulung PeakStore
09.10.2025
-
maintenance München
29.10.2025 - 30.10.2025
Kompendium
Alterung
Alterung dagegen ist eine Gebrauchswertminderung unter zeitlich wirkenden Einflüssen. Insbesondere spielt Alterung für thermisch belastete Anlagen eine große Rolle. Für mechanische Komponenten spielt Alterung bei sachgemäßem Gebrauch eine untergeordnete Rolle. Schmiermittel allerdings unterliegt der Alterung.
Amplitude
siehe Spektralanalyse
Amplitudenmodulation
Neben der Superposition spielt die Amplitudenmodulation, die multiplikative Verknüpfung von Signalen, eine wesentliche Rolle. Im einfachsten Fall wird ein hochfrequentes Trägersignal mit der Frequenz
, der Amplitude
und der Phase
mit einem niederfrequenten Modulationssignal
mit den Parametern
,
und
multiplikativ verknüpft. Aus der Nachrichtentechnik ist eine Formulierung bekannt, die auch realen Maschinendiagnosesignalen sehr nahe kommt. Sie entspricht obiger Gleichung, wenn der Modulierenden ein Gleichanteil überlagert ist:
Bei der Frequenzanalyse eines modulierten Signals mittels FFT wird die Modulierende als Seitenbänder (eigentlich Seitenlinien, "Seitenbänder" hat sich etabliert) des Trägersignals an den Stellen und
abgebildet. Zusätzlich entsteht eine Spektrallinie mit der Frequenz des Trägersignals, auf deren Größe sich die Amplitude des Trägers auswirkt.
Im Bild sieht man das Ergebnis der multiplikativen Verknüpfung von zwei Sinussignalen. Die Darstellung gehorcht der Funktion
.
Das heißt, es werden dieselben Sinusfunktionen verwendet, die bereits zur Beschreibung der Superposition verwendet wurden.
Anlagenverfügbarkeit
Applikation einer DMS-Messstelle
siehe DMS-Applikation
Ausfallmethode
siehe Operative InstandhaltungAusrichtfehler
Fehlerhafte Ausrichtung zwischen Maschinenwellen wird je nach Bauform in gewissem Maße von der Kupplung kompensiert. Übersteigt jedoch die Fehlausrichtung die Kompensationsfähigkeit der Kupplung, entstehen zusätzliche Belastungen für die beteiligten Maschinenelemente. Das sind:
- erhöhte statische und dynamische Lagerkräfte,
- erhöhte Wellenbiege- und Torsionsmomente und
- Axialkräfte.
Daraus entstehen neben erhöhten Temperaturen an den Lagern und Kupplungselementen insbesondere Schwingungen durch die Wellenverformung und die Ausgleichsbewegungen in der Kupplung. Diese Schwingungen haben einen harmonischen Charakter und sind an die Drehfrequenz der fehlausgerichteten Wellen und Vielfache dieser Frequenz gebunden.
Zur Beschreibung des Ausrichtzustands unterscheidet man zwischen:
- Axialversatz
- Winkelversatz
- Radialversatz.
Die zulässigen Abweichungen werden vom Kupplungshersteller angegeben. Beachten muss man jedoch die unter Umständen erheblichen Verlagerungen der auszurichtenden Wellen während des Betriebes.
Ausrichtfehler können durch eine Schwingungsdiagnose festgestellt und durch das Ausrichten behoben werden.
Im Schwingungssignal äußern sich Ausrichtfehler durch sinusförmige Schwingungen mit der Drehfrequenz und deren Harmonischen (Vielfachen).
Im Spektrum des Schwingungssignals findet man bei elastischer Kupplung beispielsweise eine Spektrallinie bei der Drehfrequenz und der 2. Harmonischen.
Bei starrer Kupplung findet man dagegen oft die Drehfrequenz und deren 1. Harmonische.
Außenringschaden
siehe WälzlagerschadenAußenringüberrollfrequenz
siehe WälzlagerkinematikBeschleunigungssensor
siehe Piezoelektrischer BeschleunigungssensorDehnmessstreifen
Dehnungsmessstreifen, Dehnmessstreifen oder kurz DMS wurden 1938 in Massachusetts, USA, von Arthur Claude Ruge erfunden. Sie basieren auf einem simplen physikalischen Prinzip. Jeder elektrische Leiter besitzt nämlich einen elektrischen Widerstand. Dieser ist abhängig von Material, Temperatur und den geometrischen Abmessungen des Leiters. Uns interessieren die Abmessungen, da Material und Temperatur während einer Messung praktisch konstant sind:
- Bei steigender Länge des Leiters wird der elektrische Widerstand größer.
- Bei steigendem Querschnitt des Leiters wird der elektrische Widerstand kleiner.
Daraus folgt, wenn ein elektrischer Leiter gestreckt wird, sich also seine Länge vergrößert und sich gleichzeitig sein Querschnitt verringert, steigt der Widerstand. Und solange dies im elastischen Bereich erfolgt, funktioniert es auch umgekehrt. Wenn der elektrische Leiter gestaucht wird, sich seine Länge also verkürzt und sich sein Querschnitt vergrößert, so vermindert sich sein elektrischer Widerstand. Dieser Effekt wird für DMS genutzt.
Arthur Claude Ruge klebte einen dünnen Widerstandsdraht in Mäanderform auf ein Stück dünnes Seidenpapier. Dies befestigte er an einem Biegestab. Er verglich die Widerstandsänderung mit der tatsächlichen Dehnung. Der Vergleich zeigte, dass zwischen den Ergebnissen seines DMS und denen eines herkömmlichen Dehnungsmessgeräts gute Übereinstimmung bestand.
Heutzutage befindet sich ein hauchdünner Leiter auf einer Trägerfolie. Als Trägerfolie verwendet man beispielsweise Polyimid. Die Leiterbahn wird meist aus Konstantan gefertigt. Dieses weist eine hohe Temperaturstabilität auf.
Zur Drehmomentmessung werden Dehnmessstreifen in Hauptspannungsrichtung an einem zugänglichen Wellenabschnitt appliziert. Idealerweise werden vier Dehnmessstreifen in einer Ebene senkrecht zur Drehachse, um 90 Grad versetzt und 45 Grad zur Wellenachse verdreht angeordnet. Somit liegen jeweils zwei Dehnmessstreifen genau gegenüber. Zur Vereinfachung der Installation werden zwei Dehnmessstreifen zu einem Paar zusammengefasst. Der Markt hält für diesen Einsatzfall spezielle DMS-Paare bereit.
DIN ISO 10816-3
Der Effektivwert der Schwinggeschwindigkeit wird als Bewertung für den Maschinenzustand herangezogen. Die DIN ISO 10816-3 ist wie der Vorläufer, die VDI-Richtlinie 2056, für Antriebe in der Regel anwendbar. Sie teilt die Maschinen in unterschiedliche Gruppen ein, die die Maschinen klassifizieren.
Darüber hinaus werden die Unterbauten berücksichtigt und in zwei Gruppen eingeteilt, in starre und in weiche Aufstellung. Die Zuordnung ergibt sich aus dem Verhältnis der Elastizitäten von Maschine und Fundament. Wenn die tiefste Eigenfrequenz des Gesamtsystems aus Maschine und Unterbau in Richtung der Messung um mindestens 25 % über der wesentlichen Anregungsfrequenz liegt (das ist in den meisten Fällen die Drehfrequenz), kann der Unterbau für diese Richtung als starr bezeichnet werden. Alle anderen Unterbauten können als elastisch bezeichnet werden.
Für die Bewertung werden Zonen festgelegt. Dabei bedeuten:
Zone A: | Die Schwingungen neu in Betrieb gesetzter Maschinen liegen gewöhnlich in dieser Zone. |
Zone B: | Maschinen, deren Schwingungen in dieser Zone liegen, werden üblicherweise als geeignet angesehen, ohne Einschränkungen im Dauerbetrieb zu laufen |
Zone C: | Maschinen, deren Schwingungen in dieser Zone liegen, werden üblicherweise nicht als geeignet angesehen, ständig im Dauerbetrieb zu laufen. Im allgemeinen darf die Maschine aber für eine begrenzte Zeit in diesem Zustand betrieben werden, wenn sich eine günstige Gelegenheit für Abhilfemaßnahmen ergibt. |
Zone D: | Schwingungswerte innerhalb dieser Zone werden üblicherweise als so gefährlich angesehen, daß Schäden an der Maschine entstehen können. |
Die Vorschrift gibt auch Bildungsvorschriften für Alarm-Grenzwerte an.
Zu beachten ist bei der Überwachung von Maschinen mittels Effektivwert der Schwinggeschwindigkeit, dass dieser Wert relativ unempfindlich gegenüber energiearmen Anregungen ist und somit eine Reihe von Fehlern, beispielsweise Fehler an Wälzlagern, nur sehr unzuverlässig detektierbar sind.
DMS-Applikation
Das über eine Welle übertragene Drehmoment führt zu einer Verdrehung der Welle. Diese Verdrehung führt zu einer Dehnung an der Wellenoberfläche. Im elastischen Verformungsbereich des Wellenmaterials ist die Dehnung direkt proportional der Belastung. Die Dehnung wiederum lässt sich mittel DMS messen.
Die daraus folgende Anordnung ist im Bild zu sehen. Bei der dargestellten Anordnung und der eingezeichneten Wirkung des Drehmoments werden DMS2 und DMS4 gestreckt und DMS1 und DMS3 gestaucht.
Dehnmessstreifen ändern ihren elektrischen Widerstand proportional zur Dehnung. Da die Änderungen des Widerstandes in der Regel sehr klein sind, nutzt man die Wheatstonesche Brücke zur Verschaltung der DMS. Damit lassen sich auch sehr kleine Widerstandsänderungen genau erfassen.
Die Befestigung der DMS auf der Welle geschieht durch Kleben. Dazu muss die Welle an den Klebestellen gereinigt und vor allem entfettet werden. Eine eventuell vorhandene Oxydschicht muss entfernt werden. Das Material wird aufgerauht, chemisch neutralisiert und die Klebung kann erfolgen. Bei der Klebung werden meist unterschiedliche Flüssigkeiten, z.B. erst ein Katalysator und anschließend Klebstoff hauchdünn aufgetragen, bevor der DMS mit gleichmäßiger Kraft angedrückt wird. Der Aushärtungsprozess des Klebers wird wesentlich von Temperatur und Luftfeuchtigkeit beeinflusst.
Dieser ganze Prozess kann durchaus zwei bis drei Stunden in Anspruch nehmen. Für einfache Kurzzeitmessungen ohne besondere thermische Beanspruchung verwendet man einen kalt klebenden Sekundenkleber (Cyanoacrylat). Spezielle Befestigungsmöglichkeiten und DMS gibt es für Dauermessungen oder für Messstellen, die dann hohen Temperaturen standhalten müssen. Meist handelt es sich dabei um heiß klebende Verfahren oder sogar Verschweißungen.
Sind die DMS auf der Welle fixiert, erfolgt die elektrische Verdrahtung zu der oben genannten und abgebildeten Wheatstoneschen Messbrücke. Ist die Verdrahtung auf der Welle abgeschlossen, wird die Messstelle versiegelt. Das heißt, sie wird durch eine mechanische Abdeckung gegen mechanische Beschädigung, insbesondere das Eindringen von Flüssigkeiten und gegen thermische Beeinflussung geschützt.
Zur Applikation einer DMS-Messstelle gehört der Anschluss einer Stromversorgung sowie einer Messsignalverbindung zur Auswertetechnik. Noch vor wenigen Jahren verwendete man überwiegend Schleifringübertrager. Auf der Welle oder besser am Wellenende werden Schleifringe angebracht, die mit der Welle rotieren. Der Stator besteht aus Kohlebürsten, die im ständigen Kontakt mit den rotierenden Schleifringen stehen. So ist eine unmittelbare Übertragung von Speisespannung und Messsignalen möglich. Die Verwendung von Schleifringübertragern bereitete jedoch auch Probleme. Erstens brauchte man viel Platz für die Installation bzw. überhaupt ein freies Wellenende. Zweitens war der Übergangswiderstand vergleichsweise hoch und schwankte zudem, was auf geometrische und Abweichungen in der Leitfähigkeit zurückzuführen ist. Bei höheren Drehzahlen kam es zu Übertragungsproblemen durch Abheben der Bürsten vom Schleifring. Aussetzer waren die Folge. Drittens unterliegt das gesamte System beträchlichem Verschleiß.
Seit man Sender so klein bauen kann, dass sie problemlos auf der Welle plaziert werden können, verwendet man Telemetrien zur drahtlosen Übertragung von Messwerten von rotierenden Teilen. Dabei werden die Messdaten als Modulationssignal einem auf der Welle angeordneten FM-Sender (FM = Frequenzmodulation) zugeleitet. Die elektromagnetischen Wellen werden von einem Empfänger in ein weiterverarbeitbares Signal zurück gewandelt.
Die Spannungsversorgung der Messbrücke kann durch eine Batterie erfolgen, die ebenfalls auf der Welle befestigt wird und mit rotiert. Für Langzeitmessungen, bei denen eine Batterie nicht die erforderliche Kapazität aufweisen würde, verwendet man die induktive Spannungsversorgung. Eine feststehende Spule wird mit einem vergleichsweise niederfrequenten Signal, meist im Kilohertzbereich, versorgt. Diese Spule befindet sich in direkter räumlicher Nähe zur Welle. Auf der Welle ist eine Induktionsspule plaziert, die meist aus nur einer Windung besteht. In ihr wird infolge des Induktionsprinzips eine Spannung induziert, die die Messbrücke versorgt (Trafoprinzip). Der Wirkungsgrad dieser Konstruktion ist vergleichsweise gering. Folglich besteht der Nachteil darin, dass die Statorelektronik räumlich sehr dicht an der rotierenden Welle installiert werden oder eine unverhältnismäßig Leistung aufweisen muss. Mit der Batterieversorgung lassen sich dagegen große Abstände realisieren.
Die Applikation schließt mit der Kalibrierung der Messstelle ab. Kalibriert wird direkt oder mit einer Massverkörperung. Direkt kalibrieren bedeutet, dass man die Welle mit einem genau bekanntem Prüfmoment beaufschlagt. Da das in den wenigsten Fällen möglich ist, nutzt man den Weg der Massverkörperung. Das heißt, man simuliert eine Dehnung der Wellenoberfläche und damit ein Drehmoment indem man einem Brückenwiderstand einen Präzisionswiderstand parallelschaltet. Der (englische) Fachbegriff lautet "shunten". Damit erzeugt man ein Brückenausgangssignal, welches einer Dehnung bzw. einem Drehmoment entspricht. Natürlich ist diese Art der Kalibrierung nicht so genau wie die direkte Kalibrierung. Für die meisten Messaufgaben ist diese Methode aber hinreichend genau. Eine direkte Kalibrierung ist auf jeden Fall erforderlich, wenn Genauigkeiten im Promillebereich benötigt werden, also z.B. bei Wirkungsgradbestimmungen an Zahnradgetrieben. Auf eine Kalibrierung kann verzichtet werden, wenn es nur um die Bestimmung des dynamischen Anteils geht, beispielweise bei reinen Torsionsschwingungsanalysen.
Drehmomentmessung
Die Kenntnis des Drehmomentverlaufs einer Arbeitsmaschine in Abhängigkeit von der Zeit bzw. der Drehzahl ist die entscheidende Grundlage für die sichere und gleichzeitig wirtschaftliche Bemessung eines Antriebs. Um mehr Informationen über das wirkliche übertragene Drehmoment eines Antriebs zu bekommen, wird oft der Motorstrom gemessen und mittels Spannung und Wirkungsgrad die Leistung berechnet. Unter Berücksichtigung der Drehzahl ist dann schnell das Drehmoment ermittelt. Allerdings fließen in den Motorstrom keine hochdynamischen Vorgänge ein, das heißt kurze Drehmomentspitzen und Schwingungen sind im Motorstromsignal oft überhaupt nicht zu finden.
Um wirklich den exakten Drehmomentverlauf eines Antriebs zu bestimmen, muss man das Drehmoment an der Abtriebswelle oder wenigstens an der Antriebswelle des Getriebes messen. Dazu bieten sich grundsätzlich zwei Wege an. Entweder man installiert eine Drehmomentmesswelle oder Drehmomentmessscheibe, wobei dies in der Regel kleine konstruktive Veränderungen am Antrieb erfordert oder man installiert eine DMS (Dehnmessstreifen) -Messstelle auf einem zugänglichen Stück Welle. Die zweite Variante ist für einen bereits fertig installierten, in Betrieb befindlichen Antrieb meist die einzige Möglichkeit. Sie erfordert minimale Eingriffe ins Betriebsgeschehen und zieht keine bleibenden Veränderungen am Antrieb nach sich.
Die Applikation einer Drehmomentmessstelle nimmt etwas Zeit in Anspruch und sollte von entsprechendem Fachpersonal erledigt werden.
Die Datenerfassung wird durch die Messaufgabe vorgegeben. Ist die Messstelle einmal installiert, können alle erdenklichen Arbeitssituationen erfasst werden.
Dementsprechend erfolgt dann auch die Analyse der Messdaten als Zeitschrieb oder für statistische Zwecke als Klassierungsmatrix.
Im Bild ist der Drehmomentverlauf während eines unplanmäßigen Abschaltvorgang eines Antriebs dargestellt. Durch diese Darstellung wird klar, dass das Drehmoment kurz vor der Abschaltung einen starken dynamischer Anteil aufwies.
Für die Analyse ausschließlich dynamischer Anteile im Drehmoment verwendet man die Torsionsschwingungsanalyse.
DVS-Analyse
Es ist eine uralte Aufgabenstellung mit inzwischen vielen ausgezeichneten Lösungen: Eine Maschine zu erfinden, die dem Menschen die Arbeit abnimmt und dabei Zusammenhänge genauso komplex betrachtet, wie der Mensch das tut.
Ein Diagnostiker, ein Mensch also, sieht ein Spektrum an und erkennt sehr schnell Auffälligkeiten. Wie der Mensch das genau macht, ist nur in Ansätzen bekannt. Sicher haben persönliche Erfahrungen und Intuition einen großen Einfluss.
Bei der DVS-Analyse werden die vielen Linien im Spektrum als statistische Masse betrachtet. Ihnen wird unterstellt, dass ein kleiner Teil der Linien nicht den Regeln gehorcht, also Ausreißer sind. Diese Ausreißer werden gesucht, indem für jedes Spektrum eine Signifikanzschwelle berechnet wird, welche quasi eine zulässige Amplitude darstellt. Die Berechnung erfolgt so, dass immer ein kleiner Teil, die Ausreißer, nicht ins Schema passen, also zu groß für die Signifikanzschwelle sind.
Im nächsten Schritt werden alle Linien außer den Ausreißern verworfen. Die Ausreißer allerdings werden nun daraufhin überprüft, ob sie von der Frequenz her zu einem möglichen Schadensmuster passen.
Effektivwert der Schwinggeschwindigkeit
siehe DIN ISO 10816Ermüdung
Ermüdung ist die Trennung von mikroskopischen und makroskopischen Stoffteilchen aus der Oberflächenschicht eines Körpers heraus.
- Hertz’sche Pressung führt zu einem Spannungsmaximum unter der Oberfläche.
- Es kommt zum Anrisse unter der Oberfläche.
- Der Riss schreitet fort.
- Es kommt zum Restbruch beim Abwälzen zweier kräftegebundener Oberflächen.
Faltung
siehe StoßimpulsFFT
siehe SpektralanalyseFouriertransformation
siehe SpektralanalyseFrequenz
Außenringfrequenz, Innenringfrequenz, Wälzkörperspinfrequenz, Käfigrotationsfrequenzsiehe Wälzlagerkinematik
Getriebekinematik
Bei Zahnradgetrieben ergibt sich die Zahneingriffsfrequenz aus dem Produkt der Drehfrequenz mit der Zähnezahl. Das gilt für gerad- oder schrägverzahnte Stirnradgetriebe, Kegelradgetriebe wie für Schneckengetriebe.
Bei Planetengetrieben (eigentlich Umlaufrädergetriebe) bezeichnet man das zentrale Ritzel als Sonne und die Räder mit den umlaufenden Achsen als Planeten. Die Planeten sitzen auf dem Planetenträger, dem Steg. Häufig wird ein Rad innenverzahnt (Hohlrad) und als Gehäuse genutzt.
Beispielhaft werden hier für das häufig vorkommende einstufige Planetengetriebe mit feststehendem Hohlrad die Formeln angegeben.
Ist die Drehfrequenz der Sonne gegeben, berechnet sich die Drehfrequenz des Steges nach
und die Spinfrequenz des Planetenrades nach
(Indizes: 1 - Sonne, 2 - Planetenrad, 3 - Hohlrad, 4 - Steg)
Die Zahneingriffsfrequenz berechnet sich nach
Darüber hinaus ergeben sich Frequenzen für das Überrollen einer Unregelmäßigkeit auf dem Sonnenritzel
(k bezeichnet die Anzahl der Planetenräder),
für das Überrollen einer Unregelmäßigkeit auf dem Hohlrad und
für das Überrollen einer Unregelmäßigkeit auf dem Planetenrad
.
Fertigungsbedingt gibt es bei Zahnrädern die Geisterfrequenz (auch Maschinenfrequenz):
,
mit - Zähnezahl des Referenzrades.
Gewaltnutzung
siehe SchädigungsmechanismenGleitverschleiß
siehe VerschleißHarmonische Ausrichtfehler
siehe AusrichtfehlerHarmonischer umlaufender Verzahnungsschaden
siehe Umlaufender VerzahnungsschadenHertz'sche Pressung
siehe ErmüdungHilberttransformation
siehe HüllkurvenanalyseHüllkurvenanalyse
Die Hüllkurvenanalyse ist ein Werkzeug, mit dem Stoßimpulse bzw. Stoßimpulsfolgen extrahiert werden können. Das gefaltete Signal ist - von Signalverfälschungen durch Schalltransport abgesehen - zwar an der Oberfläche der Maschine unmittelbar messbar. Unterzieht man es einer Spektralanalyse, findet man aber lediglich die Eigenfrequenzen des Systems. Um das ursprüngliche Ereignis, nämlich die Stoßfolge, deutlich sichtbar machen zu können muss der bei der Signalentstehung erfolgte Prozess der Faltung in geeigneter Weise umgekehrt werden, um die Erregerfunktion von den Eigenfrequenzen wieder zu trennen. Dazu bietet sich die Hüllkurvenanalyse an.
Die Bildung der Hüllkurve kann auf verschiedenen Wegen erfolgen. Die analoge oder digitale Gleichrichtung ist dabei ebenso geeignet wie die Hüllkurvenextraktion mittels Hilberttransformation. Man muss sich vorstellen, dass die positiven Spitzen des Signals miteinander verbunden werden, so als ob eine Hülle über das ganze gelegt wird. Mitunter ist eine nachfolgende Datenverdichtung ratsam, aber nicht zwingend erforderlich. Störsignalanteile lassen sich vor der Hüllkurvenbildung beispielsweise mit einem geeigneten Hochpassfilter eliminieren.
Die Hüllkurve kann dann mittels FFT einer Spektralanalyse unterzogen werden. So entsteht das Hüllkurvenspektrum. Im Hüllkurvenspektrum sieht man nun eindeutig die Stoßimpulswiederholfrequenz bei 100 Hz sowie die Harmonischen (Höherfrequenten) dazu. Die im Bild erkennbaren Seitenbänder resultieren daraus, dass die Stoßimpulsfolge amplitudenmoduliert war.
Die hochpassgefilterte Hüllkurvenanalyse ist somit ein Werkzeug, um harmonische Anregungen von Stoßanregungen zu unterscheiden.
Innenringschaden
siehe WälzlagerschädenInnenringüberrollfrequenz
siehe WälzlagerkinematikInspektion
Unter Inspektion werden alle Maßnahmen zur Feststellung und Beurteilung des Istzustandes von technischen Mitteln eines Systems verstanden. Das beinhaltet im wesentlichen die visuelle Inspektion, das Messen des Verschleißes und die Suche nach Mängeln. Im gegebenen Kontext sind die Begriffe Inspektion und Maschinendiagnose Synonyme.Instandhaltung
Die Instandhaltung ist in der DIN 31051 definiert und besteht aus der Wartung, der Inspektion, der Instandsetzung und der Verbesserung von technischen Mitteln eines Systems.
Wartung
Unter Wartung versteht man die Maßnahmen zur Verzögerung des Abbaus des vorhandenen Abnutzungsvorrats.
Inspektion
Unter Inspektion werden alle Maßnahmen zur Feststellung und Beurteilung des Istzustandes von technischen Mitteln eines Systems verstanden. Das beinhaltet im wesentlichen die visuelle Inspektion, das Messen des Verschleißes und die Suche nach Mängeln. Im gegebenen Kontext sind die Begriffe Inspektion und Maschinendiagnose Synonyme.
Instandsetzung
Unter Instandsetzung werden alle Maßnahmen zur Wiederherstellung des Sollzustandes von technischen Mitteln eines Systems verstanden.
Verbesserung
Unter Verbesserung wird die Kombination aller technischen und administrativen Maßnahmen sowie Maßnahmen des Managements zur Steigerung der Funktionssicherheit einer Betrachtungseinheit, ohne die von ihr geforderte Funktion zu ändern, verstanden.
Instandhaltungsstrategien
Um Kosten und Nutzen der Instandhaltung in einem vertretbaren Verhältnis zu halten, stellt sich die Frage nach der richtigen Instandhaltungsstrategie. Diese Betrachtung wird anschaulich, wenn man bedenkt, dass neben den reinen Inspektion- und Instandsetzungskosten Kosten infolge der Nichtverfügbarkeit von Produktionsanlagen (Produktionsausfallkosten) anfallen.
In der Praxis findet man drei grundsätzliche Instandhaltungsstrategien, die die Möglichkeiten der Kostenbeeinflussung darstellen, die operative, die vorbeugende und die zustandsorientierte Instandhaltung.
Instandsetzung
siehe InstandhaltungIntegration
siehe Physikalische MessgrößeKäfigrotationsfrequenz
siehe WälzlagerkinematikKäfigschaden
siehe WälzlagerschädenKennwertüberwachung
siehe SchwingungskennwertüberwachungKorrosion
Korrosion ist eine durch elektrochemische oder chemische Reaktionen herbeigeführte Werkstoffveränderung an der Oberfläche und im inneren Werkstoffgefüge in bestimmter Umgebung.
- Lochfraß- und Kontaktkorrosion bilden sich vor allem bei längerem Maschinenstillstand.
- Spannungsrisskorrosion tritt auf, wenn gleichzeitig Zugspannungen wirken, Unstetigkeiten in der Metalloberfläche sind Ausgangsstellen.
- Schwingungsrißkorrosion tritt an wechselbeanspruchten Bauteilen auf.
- Reibkorrosion ist die Folge von kleinen Relativbewegungen zweier sich berührender Körper. Stillstandsmarkierungen sind die Folge von Korrosion in Kombination mit Verschleiß.
Ladungsverstärker
siehe Piezoelektrischer BeschleunigungssensorLagersitzprobleme
siehe Lose TeileLokaler Verzahnungsschaden
Neben dem Zahnbruch konzentrieren sich insbesondere Zahnflankenermüdungserscheinungen, Deformationen und Dauerbruchanrisse auf einen oder wenige Zähne. Ist lediglich ein Zahn von n Zähnen geschädigt, so gestaltet sich der jeweils n-te Zahneingriff mit höherer oder aber verminderter Intensität. Für die Signalanalyse heißt das, dass die gleichmäßige Zahneingriffsschwingung einmal pro Umdrehung gestört wird. Das heißt, die Zahneingriffsschwingung wird mit der Drehbewegung des defekten Zahnrades amplitudenmoduliert. Dazu kommt, dass sich die Winkelgeschwindigkeit der Zahnräder geringfügig ändern kann, und es somit darüber hinaus zu einer Frequenzmodulation kommt.
Sind mehrere Zähne geschädigt, gilt analoges. Praktisch ist der lokale Charakter von Verzahnungsschäden gegeben, solange nicht alle Zähne geschädigt sind.
Verzahnungsschäden äußern sich im Spektrum des Signals. Man erkennt die durch den lokalen Verzahnungsschaden hervorgerufene Modulation als Seitenbänder zur Zahneingriffsfrequenz. Der Abstand des Seitenbandes zur Zahneingriffsfrequenz bezeichnet die Drehfrequenz des geschädigten Zahnrades. Es ist somit exakt zuzuordnen. Die Seitenbänder ihrerseits können Harmonische, also Vielfache, aufweisen.
Im Bild erkennt man verschiedene Seitenbänder, die tatsächlich zwei verschiedene Schäden bezeichnen.
Quelle der beiden Bilder: Wirth, R.: Maschinendiagnose an Industriegetrieben. Teil II: Signalidentifikation in der Praxis. Antriebstechnik 37(1998), Nr. 11, S.77-81
Lokaler Wälzlagerschaden
Typische lokale Wälzlagerschäden sind Riefen, Ausbrüche, Pitting, Stillstandsmarkierungen und Ausschälungen auf der Laufbahn der Lagerringe und an Wälzkörpern.
Wird der Schaden überrollt, also kraftschlüssig passiert, so äußert sich das in einem Stoßimpuls. Das wiederholte periodische Auftreten der von Stoßimpulsen ist im Hüllkurvenspektrum nachweisbar. Die Stoßimpulswiederholfrequenz ergibt sich aus der Wälzlagerkinematik.
Bild: Außenringschaden
Bild: Spektrum
Bild: Hüllkurvenspektrum
Für einen Außenringschaden sind das Spektrum und das Hüllkurvenspektrum abgebildet. Im Hüllkurvenspektrum ist die Außenringüberrollfrequenz eindeutig nachweisbar. Im Spektrum dagegen gelingt dieser Nachweis nur durch die etwas umständliche Betrachtung der Höherharmonischen.
Befindet sich der Schaden in Relativbewegung zur Lastzone eines Wälzlagers, handelt es sich um einen umlaufenden lokalen Wälzlagerschaden.
Lose Teile
Die vier Phänomene lose Teile, lose Verbindungen, Passungsrost und Wellenanriss werden hier, obgleich die Ursache sehr verschieden sein kann, zusammen betrachtet, da sie aus diagnostischer Sicht zunächst nicht trennbar sind.
Fremdkörper, die sich um die Welle gewickelt haben, oder aber Teile an der Welle, die sich gelöst haben, können einmal pro Umdrehung an Statorteile anschlagen. Ähnliches geschieht, wenn Fremdkörper in den Aktionsbereich rotierender Teile hinein geführt werden. In diesen Fällen treten Stöße zwischen sich drehenden und ruhenden Komponenten auf.
Der gleiche Effekt tritt auf,
- wenn Bauteile, die auf der Welle fehlerhaft montiert sind und arbeiten,
- bei Passungsrost zwischen auf der Welle montierten Teilen und der Welle,
- wenn die Welle angerissen ist und ihre Biegesteifigkeit folglich über den Azimut variiert oder
- wenn fehlerhaft montierte Wälzlager in ihrem Sitz arbeiten.
Vorausgesetzt, die Welle unterliegt einer radialen Belastung, wird sich durch die Rotation der Welle einmal pro Umdrehung ein - wenn auch kleiner - Spalt auftun und wieder schließen. Entsprechend der Drehfrequenz wird sich dieser Vorgang mehrmals pro Sekunde wiederholen, was zu Aufprallgeschwindigkeiten führt, die einem Stoßimpuls entsprechen. Und genauso ist die Wirkung auf die umgebende Maschine. Wir detektierten eine Stoßimpulsfolge mit der Drehfrequenz.
Stoßimpulsfolgen können wir im Hüllkurvenspektrum sichtbar machen.
Im Hüllkurvenspektrum erkennt man deutlich, dass der Drehfrequenzpeak im enormer Intensität auftritt. Ursache war - wie nach der Demontage eindeutig klar wurde - ein Wellenschaden im Bereich der Passfeder.
Quelle der beiden Bilder: Wirth, R.: Maschinendiagnose an Industriegetrieben. Teil II: Signalidentifikation in der Praxis. Antriebstechnik 37(1998), Nr. 11, S.77-81
Lose Verbindungen
siehe Lose TeileModulation
siehe AmplitudenmodulationNormalbeanspruchung
siehe SchädigungsmechanismenOperative Instandhaltung
Die operative Instandhaltung sieht die Instandsetzung nach Ausfall vor. Sie wird daher gelegentlich auch "Ausfallmethode" genannt. Jedes Bauteil bleibt so lange in Betrieb bis es ausfällt und wird dann instandgesetzt bzw. ausgewechselt.
Die operative Instandhaltung scheint zunächst die preiswerteste Methode zu sein, da wirklich nur gewechselt wird, was defekt ist. Somit wird die Abnutzungsreserve eines jeden Bauteils tatsächlich verbraucht. Sie liefert aber die geringste Betriebssicherheit, was sich auf die Anlagenverfügbarkeit auswirken kann und somit Produktionsausfallkosten verursacht. Ein typisches Beispiel ist die Glühlampe in Wohnräumen, die wir gewöhnlich erst wechseln, wenn sie defekt ist.
Ordnungsanalyse
Schädigungsereignisse an Antrieben äußern sich in der Regel durch periodische Schwingungen, die einen Bezug zur Drehzahl des Antriebs haben. Die Schwingungserfassung sowie die Schwingungsdiagnose dagegen erfolgen meist zeitabhängig.
Zur besseren Bewertung von Schwingungssignalen verwendet man Verfahren der Signaltransformation zur Umwandlung in den Frequenzbereich. Im einfachsten Fall bildet man das Frequenzspektrum. Im Spektrum wird die Amplitude als Funktion der Frequenz dargestellt. Die Einheit der Abszisse ist Hertz.
Bei Antrieben mit konstanter Drehzahl lassen sich aus den Messdaten direkt die erforderlichen Spektren erzeugen. Dies ist bei Antrieben mit variabler Drehzahl nicht der Fall. Hier werden die Messdaten zunächst einer Ordnungsanalyse unterzogen.
Bei der Ordnungsanalyse wird ein zeitsynchrones Signal auf die Drehzahl normiert, so dass ein drehzahlsynchrones Signal entsteht. Die weitere Bewertung kann dann in gewohnter Art und Weise erfolgen. Die Einheit der Abszisse ist die Ordnung.
Eines der anerkannten, leicht anwendbaren Verfahren ist das Resampling. Erst nach der Datenerfassung findet das rein rechnerische Neuabtasten des Schwingungssignals statt. Dazu ist die Kenntnis der exakten Drehzahl zu jedem Zeitpunkt der Datenerfassung erforderlich. Das heißt, zu den oben genannten Kanälen, dem Zeitkanal und dem Schwingungskanal, muss ein zusätzlicher, dritter Kanal aufgezeichnet werden, der die Augenblickswerte der Drehzahl zu jedem Abtastzeitpunkt enthält. Rein rechnerisch wird dann aus dem Zeitsignal ein drehzahlsynchrones Signal gebildet.
Alle Geräte der GfM beherrschen Ordnungsanalyse per Resampling.
Passungsrost
siehe Lose Teilepeak-to-peak-Amplitude
siehe SpektralanalysePeakamplitude
siehe SpektralanalysePhysikalische Messgröße
Sensoren können Schwingbeschleunigung, Schwinggeschwindigkeit oder Schwingweg erfassen. Aber unabhängig davon, welche physikalische Größe der Aufnehmer erfasst, ist die Darstellung der Schwingung ebenfalls als Beschleunigung, Geschwindigkeit oder Weg informationsadäquat möglich, denn es gilt:
bzw.
- Schwingweg
- Schwinggeschwindigkeit
- Schwingbeschleunigung
- Zeit.
Die Darstellungsform von Schwingungen, insbesondere von Schwingungsspektren, ist ein häufiger Diskussionspunkt. Die Beschleunigung ist der Kraft proportional. Demgegenüber lässt sich aus der Geschwindigkeit auf die Energie schließen.
Praktische Bedeutung hat, dass in die Umrechnung von einer in die andere physikalische Größe die Frequenz eingeht. Für eine Sinusschwingung gilt:
bzw.
Die Frequenz steht also im Nenner. Das hat zur Folge, daß hochfrequente Signalanteile bei der Verwendung der Schwinggeschwindigkeit gegenüber der Schwingbeschleunigung unterbewertet werden. Bei der Verwendung des Schwingweges quadriert sich dieser Einfluss.
Im Bild handelt es sich um exakt dasselbe Spektrum, das jedoch einmal als Beschleunigungs-, einmal als Geschwindigkeit- und einmal als Wegspektrum dargestellt wird.
Piezoelektrischer Beschleunigungssensor
Die Arbeitsweise des piezoelektrischen Beschleunigungssensors basiert auf dem 1880 von J. und P. Curie entdeckten Effekt, dass sich Quarzkristalle unter mechanischer Belastung (Druck, Zug, Torsion) senkrecht zu den polaren Achsen aufladen.
Eine seismische Masse ist nur durch den Piezokristall mit dem Sensorgehäuse mechanisch verbunden.
Je nach Anordnung unterscheidet man in Dickenschwinger, Biegeschwinger und Scherschwinger. Für die Erfassung von Schwingungen in vorzugsweise einer Messrichtung hat sich der Scherschwinger zum Favoriten entwickelt.
Wird der gesamte Sensor in Bewegung versetzt, wirken aufgrund der Trägheit der seismischen Masse Scherkräfte auf den Piezokristall. Der Kristall erzeugt daraufhin eine Ladung, die der Scherkraft proportional ist.
Der nutzbare Übertragungsbereich dieser Sensor ist durch eine untere und eine obere Bandgrenze eingeschränkt. Die untere Grenze liegt bei einigen Zehntel Hertz. Die obere Grenze liegt über der Resonanzfrequenz des Sensors. Die Resonanzfrequenz liegt je nach Bauart meist zwischen 5 und 100 kHz. Als nahezu linearer Messbereich steht das erste Drittel des Übertragungsbereichs bis zur Resonanzfrequenz zur Verfügung, wobei die Resonanzfrequenz des Messaufbaus sehr von der Befestigung des Sensors abhängt und auf jeden Fall unter der angegebenen Resonanzfrequenz des Sensors liegt. Untersuchungen im Hörschallbereich können mit Beschleunigungssensoren problemlos realisiert werden.
Die im Sensor erzeugte Ladung wird mit Hilfe eines Sensorkabels in Zweileitertechnik einem Ladungsverstärker zugeführt. Wegen der geringen Ladung im Bereich von einigen pC dürfen die Kabel eine bestimmte Länge, meist 4 m, nicht überschreiten.
Bei moderneren Sensoren ist der Ladungsverstärker im Sensorgehäuse integriert. Hier kann dann die Kabellänge über 100 m betragen. Allerdings muss der Ladungsverstärker mit Elektroenergie versorgt werden. Dies realisiert man ebenfalls in Zweileitertechnik dadurch, dass von Seiten des Messgeräts ein konstanter Gleichstrom eingespeist wird. Das Messsignal wird dem Gleichstrom überlagert und im Messgerät mittels Hochpassfilter wieder separiert. Da der in piezoelektrischen Beschleunigungssensor integrierte Verstärker sowieso keine Gleichanteile erfassen kann, stellt diese Verfahrensweise keine Einschränkung der Funktionalität dar. Der Eingang des Messgeräts muss natürlich so beschaffen sein, dass die Stromversorgung und eine Einrichtung zum Herausfiltern des Messsignals vorgesehen sind.
Für Ultraschallmessungen nutzt man zum Teil bewußt den Bereich oberhalb der Resonanzfrequenz. Einige Messgeräte oder Messverfahren nutzen ausschließlich den Resonanzbereich.
Produktionsausfallkosten
siehe InstandhaltungsstrategienResonanz
siehe TorsionsschwingungsanalyseResonanzschaubild
siehe TorsionsschwingungsanalyseRMS-Amplitude
siehe SpektralanalyseRollverschleiß
siehe VerschleißSchädigungsmechanismen
Man unterscheidet zwischen Normalbeanspruchungs- und Überbeanspruchungsmechanismen. Die Normalbeanspruchungsmechanismen wirken während der Nutzung einer Maschine. Zu ihnen gehören Verschleiß, Ermüdung, Alterung und Korrosion. Die Überbeanspruchungsmechanismen wirken dagegen bei Gewaltnutzung und beinhalten Riss, Bruch, Stromdurchgang sowie unplanmäßige thermische bzw. chemische Einflüsse.Schwingbeschleunigung
siehe Physikalische MessgrößeSchwinggeschwindigkeit
siehe Physikalische MessgrößeSchwinggeschwindigkeit - Effektivwert nach DIN ISO 10816
siehe DIN ISO 10816Schwingungsdiagnose
Der Schwingungsdiagnose liegt der einfache Zusammenhang zugrunde, dass alle mechanischen Vorgänge in Maschinen - eingeschlossen Unregelmäßigkeiten an Komponenten bis hin zu Schäden - Kraftumsetzungsprozesse zur Folge haben, die in der Maschine weitergeleitet werden und letztlich an die Gehäuseoberfläche gelangen. Sie haben periodischen Charakter, das heißt sie treten in festen Zeitabständen immer wieder auf.
Am einfachsten vorstellbar ist dies an einer lokalen Unregelmäßigkeit an einem Wälzlageraußenring. Alle Wälzkörper passieren diese schadhafte Stelle und verursachen je einen Kraftstoß. Ein ähnlicher Effekt tritt auf, wenn an einer Getriebestufe ein Zahn nicht voll trägt. Der folgende Zahn muss die nicht übertragene Energie "auffangen", was ebenfalls einen Kraftstoß zur Folge hat.
Eine Maschine verursacht in der Regel eine Vielzahl von Einzelschwingungen, deren Summe einfach als Lärm wahrnehmbar ist. Sehr versierte Fachleute mit langer Betriebserfahrung können aus diesem Lärm mit Hilfe des Gehörs ohne Hilfsmittel den Maschinenzustand ableiten. Einem Neuling wird das kaum gelingen. Der Einsatz moderner Signalanalysetechnik erweist sich hier als brauchbares Hilfsmittel.
Ganz neu ist das nicht. Schließlich findet man schon in [N. N.; FAG Kugelfischer: Zum Erkennen der Schadensursache bei Wälzlagern. Wälzlagertechnik (1964)3, S. 19 - 21] folgenden Text: "Vielfach erkennt man Lagerschäden daran, dass sich das Laufgeräusch verändert. In diesem Fall sollte man versuchen, das Geräusch zu beschreiben, z.B. durch Angaben wie: gleichmäßig oder schwellend, periodisch oder ungleichmäßig, brummend, pfeifend, singend, klopfend. Stellt man eine regelmäßig wiederkehrende Folge von Geräuschen fest, so versuche man zu beschreiben, mit welcher Frequenz sie auftritt. ... Bei niedrigen Drehzahlen hat es sich häufig bewährt, mit einem Bleistift im Rhythmus des Geräusches auf ein Blatt Papier zu klopfen und nach einer bestimmten Anzahl von Sekunden die Punkte auszuzählen." Die moderne Maschinendiagnose nutzt dieselben Zusammenhänge. Nur sind die Werkzeuge inzwischen andere.
Anwendung findet die Schwingungsdiagnose, um folgende Phänomene zu erkennen:
- Unwucht,
- Ausrichtfehler
- anschlagende lose Teile, Passungsprobleme, Wellenschäden
- lokale Verzahnungsschäden
- umlaufende Verzahnungsschäden
- lokale Wälzlagerdefekte
- umlaufende Wälzlagerdefekte
- elektrische Effekte
- Schaufeleffekte an Lüftern und Pumpen
- Oil-whirl an Gleitlagern
Die Schwingungsdiagnose wird oft auf die Gehäuseschwingungsdiagnose reduziert, bei der also mit Hilfe eines geeigneten Sensors die Oberflächenschwingung eines Maschinengehäuses aufgezeichnet und anschließend analysiert wird. Schwingungsdiagnose kann aber auch an der sich frehenden Welle durchgeführt werden. Hier sprechen wir entsprechend der physikalischen Messgröße von der Wellenschwingungsanalyse, der Drehungleichförmigkeitsanalyse oder der Torsionsschwingungsanalyse.
Lesen Sie gern auch unseren Artikel auf Wikipedia.
Schwingungskennwertüberwachung
Schwingungskennwerte sind Skalare. Sie werden aus dem Zeitverlauf der Messgröße gebildet. Sie sind geeignet, bestimmte Signaleigenschaften quantitativ zu beschreiben.
Diagnoseverfahren und -geräte, die auf der Erfassung eines Kennwerts basieren, sind einfach handhabbar. Sie können in der Regel durch nicht speziell qualifiziertes Personal angewandt werden. Die Diagnosezuverlässigkeit dieser Verfahren ist jedoch mitunter nicht ausreichend.
Ein verbreitet angewandter Diagnosekennwert ist der Effektivwert der Schwinggeschwindigkeit im Frequenzbereich zwischen 10 und 1000 Hertz. Er fand in der inzwischen nicht mehr gültigen VDI-Richtlinie 2056 ebenso Verwendung wie in der heute für die Antriebstechnik relevanten DIN ISO 10816-3.
Schwingweg
siehe Physikalische MessgrößeSeitenbänder - Amplitudenmodulation
siehe AmplitudenmodulationSeitenbänder - lokaler Verzahnungsschaden
siehe Lokaler VerzahnungsschadenSeitenbänder - umlaufernder lokaler Wälzlagerschaden
siehe Umlaufender lokaler WälzlagerschadenSpektralanalyse
Zeichnen wir beliebige Ereignisse auf, so tun wir das üblicherweise in der Reihenfolge ihres Auftretens oder aber in einer anderen relativ willkürlichen Reihenfolge.
Nehmen wir einen Teller Obst, so können wir die Früchte in der Reihenfolge, in der sie auf dem Teller liegen nennen. Das ist allerdings für eine größere Menge recht unhandlich. Deswegen bilden wir bestimmte Klassen, in unserem Beispiel sind es die Klassen "Apfel", "Zitrone", "Kirsche" und "Banane". Jetzt zählen wir, wieviele Vertreter jeder Klasse vorliegen und tragen das in ein entsprechendes System, beispielsweise eine Grafik ein.
Diese Grafik nennen wir Spektrum.
Mit Signalen tun wir exakt dasselbe. Wir zeichnen ein Signal zunächst als Zeitsignal auf. Anschließend versuchen wir, in dem Signal eindeutige Strukturen zu finden und deren Häufigkeit in einem Spektrum darzustellen. Die einfachsten Strukturen in einem willkürlichen Signal sind Sinus- und Cosinusschwingungen. Wir suchen also nach Sinus- und Cosinusschwingungen mit unterschiedlichen Frequenzen und versuchen auf diese Art und Weise das Signal als eine Summe solcher Schwingungen zu rekonstruieren.
Die Mathematik bietet hierfür die Fouriertransformation bzw. einen schnellen und speicherplatzoptimierten Algorithmus, die FFT (Fast Fourier Transformation) an.
Eine einfache Sinusschwingung, die im betrachteten Zeitfenster ganzzahlig vorhanden ist, wird im Amplitudenspektrum als eine Linie abgebildet. Dabei entspricht die Höhe der Linie der Amplitude, das heißt der maximalen Elongation, des Zeitsignals.
Hier ist die Peakamplitude abgebildet im Unterschied zur in Europa eigentlich häufiger verwendeten RMS-Amplitude, die den Effektivwert repräsentiert. Im amerikanischen Raum findet auch die peak-to-peak-Amplitude Verwendung. (RMS - root mean square; peak - Spitze)
Für Diagnosesignale, die im betrachteten Zeitfenster also nicht zwangsläufig stationär sind, gilt, dass jede einzelne Spektrallinie des Betragsspektrums ein Maß dafür ist,
- mit welcher Häufigkeit und
- mit welchen Amplituden
die entsprechende Frequenzkomponente im Zeitsignal enthalten ist.
Spektrum
siehe SpektralanalyseStillstandsmarkierungen
siehe KorrosionStoßimpuls
Besondere Bedeutung hat im Zusammenhang mit Maschinensignalen der Stoßimpuls. Impulse oder Stoßimpulse, beide Formulierungen findet man in der Diagnosepraxis, entstehen
- infolge von Wälzlagerschäden,
- infolge anschlagender loser Teile und
- unter Umständen infolge bestimmter Verzahnungsfehler.
Der Impuls ist im weitesten Sinne ein Vorgang, dessen Amplitudenwerte nur innerhalb einer beschränkten Zeitspanne merklich von Null abweichen. Innerhalb dieser Zeitspanne kann das Signal einen bestimmten Verlauf annehmen (Rechteck, Dreieck usw.). Ein Impuls kann unipolar oder bipolar (mit Vorzeichenwechsel) sein. Ein bipolarer Impuls ist der Knall in der Akustik.
Eine Sonderform des Impuls ist der Dirac-Stoß. Der Dirac-Stoß ist ein Rechteckimpuls mit der zeitlichen Ausdehnung, die gegen Null geht. Seine Amplitude geht gegen unendlich. Somit ergibt sich für das Betragsspektrum des Dirac-Stoßes der konstante Wert Eins. Das heißt, er enthält alle Frequenzen mit gleicher Energie.
Der reale, an Maschinen auftretende Stoßimpuls besitzt sowohl eine endliche Amplitude als auch eine zeitliche Ausdehnung. Dazu kommt, dass die Auslenkung des realen Stoßimpulses in der Regel nicht auf den Wert Null zurückfällt. Infolgedessen enthält der reale Stoßimpuls nur bestimmte Frequenzanteile.
Fast ausschließlich durch Faltung werden Stoßimpulse von Anregungsort fortgeleitet. Die Faltung geht vom linearen zeitinvarianten System aus. Lineare Systeme besitzen die Eigenschaft der Superposition. Besteht ein Eingangssignal aus der gewichteten Summe mehrerer Signale, so besteht das Ausgangssignal aus der Superposition, das heißt der gewichteten Summe der Ausgangssignale des Systems für jedes dieser Signale. Zeitinvarianz bedeutet, dass eine Zeitverschiebung des Eingangssignals zu einer Zeitverschiebung des Ausgangssignals führt, ohne dass sich die Signalform verändert. Ein lineares zeitinvariantes System besitzt ein Einheitsimpulsübertragungsverhalten .
Wirkt an einem schwingfähigen System ein Eingangssignal , so berechnet sich das Ausgangssignal zu:
.
Diese Gleichung bezeichnet man als Faltungsintegral oder auch Superpositionsintegral. Für die Faltung zweier Signale hat sich folgende Schreibweise durchgesetzt:
.
Stoßimpulse sind mittels Hüllkurvenanalyse zuverlässig nachweisbar.
Superposition
Harmonische Schwingungen überlagern sich durch Superposition. Unter Superposition versteht man die additive Verknüpfung von Signalen. Das heißt, zwei oder mehr Signale werden miteinander addiert.
Links im Bild sieht man von oben nach unten zwei Sinusschwingungen, dargestellt als Zeitfunktion, mit einer Frequenz von 12,2 Hz und mit einer Frequenz von 31,7 Hz. Im untersten Bild ist die Summe dieser beiden Funktionen, das heißt, die Augenblickswerte wurden schlichtweg miteinander addiert. Rechts sind die dazugehörigen Spektren abgebildet. Im untersten Bild erkennt man, dass die Superposition im Spektrum zur Abbildung von je einer Spektrallinie für jede enthaltene Frequenzkomponente führt. Die Höhe der Spektrallinien repräsentiert exakt die Amplitude der Einzelschwingungen. Die Fähigkeit, sich zu überlagern führt dazu, dass niedrige Schwingungen mit derselben Frequenz enorme Amplituden hervorrufen können.
Die Einzelschwingungen können mit ihren Amplituden im Spektrum sichtbar gemacht werden. Dabei entspricht dann die Höhe der Spektrallinie zu jeder Frequenz der (mittleren) Amplitude des betreffenden Erregersignals.
Torsionsschwingungsanalyse
Unter Torsionsschwingung versteht man die periodische Änderung des Drehmoments in Abhängigkeit von der Zeit. Torsionsschwingungen treten häufig im Zusammenhang mit Resonanzerscheinungen auf, nämlich wenn die Torsionseigenschwingung einer Welle oder eines Antriebsstrangs angeregt wird. Außerdem können technologisch bedingte oszillierende Kräfte qualitativ und quantitativ bestimmt werden.
Zur Torsionsschwingungsanalyse eines Antriebs nutzt man das hochfrequent aufgezeichnete Drehmoment. Dieses wird mittels DMS erfasst. Zuvor muss eine DMS-Messstelle appliziert werden. Das Drehmoment wird nun hochfrequent aufgezeichnet. Zeichnet man auch die Drehzahl auf, kann man anschließend auf die Leistung rückschließen.
Im Zeitsignal ist der Drehmomentverlauf beim Auslaufvorgang dargestellt. Es wird eine Torsionseigenschwingung des Systems angeregt, und das System schwingt entsprechend. Das heißt, der gesamte Antriebsstrang wird tordiert und entspannt sich wieder. Dieser Vorgang wiederholt sich alle 0,07 s, was einer Frequenz von 13,5 Hz entspricht.
Aus dem Zeitsignal wird ein Abschnitt entnommen und einer Fouriertransformation unterzogen. Im Spektrum erkennt man eine Hauptschwingungskomponente bei 13,5 Hz. Dies entspricht exakt der im Zeitsignal erkennbaren Oszillation.
Im Resonanzschaubild erkennt man Bereiche, in denen sich die diagonal verlaufenden Erregerfrequenzen mit horizontal verlaufenden Eigenfrequenzen schneiden. Zu teilweise schädlichen Resonanzerscheinungen kommt es insbesondere bei Übereinstimmung von Erregerschwingungen hoher Intensität mit ungedämpften Eigenschwingungen. Die konkrete Interpretation hängt natürlich von der Problemstellung ab.
Überbeanspruchung
siehe SchädigungsmechanismenÜberrollfrequenz
siehe WälzlagerkinematikUmlaufender lokaler Wälzlagerschaden
Im Gegensatz zum lokalen Wälzlagerschaden liefern uns bezüglich der Lastzone umlaufende lokale Schäden aus diagnostischer Sicht einige Effekte, die zu kennen für eine umfassende Diagnose erforderlich sind.
Die Relativbewegung zwischen Schaden und Lastzone führt dazu, dass der Schaden nur zeitweise kraftschlüssig passiert wird. (Das gilt natürlich nicht für vorgespannte Lager, wie wir sie beispielsweise an Spindeln von Werkzeugmaschinen finden.) Mathematisch ist dies beschreibbar durch die Amplitudenmodulation einer konstanten Stoßimpulsfolge mit einer Halbsinusfunktion.
Bei dem sehr häufigen Fall, dass der Innenring rotiert und die Lage der Lastzone konstant ist, sind es Innenringschäden und Wälzkörperschäden, die diesem Mechanismus unterliegen. Der Innenringschaden wird dann mit der Drehfrequenz der Welle moduliert, und es entstehen entsprechende Seitenbänder. Der Wälzkörperschaden wird dementsprechend mit der Käfigrotationsfrequenz moduliert, so dass Seitenbänder im Abstand der Käfigrotationsfrequenz auftreten.
Bild: Innenringschaden
Bild: Hüllkurvenspektrum zum Innenringschaden
Für einen Innenringschaden ist das Hüllkurvenspektrum abgebildet. Neben der Innenringsüberrollfrequenz sind die Seitenbänder im Abstand der Drehfrequenz nachweisbar. Darüber hinaus ist ein Drehfrequenzpeak mit Harmonischen ebenfalls vorhanden.
Unwucht
In einem rotierenden System ist definitionsgemäß dann eine Unwucht vorhanden, wenn die von den Massenelementen des Rotors erzeugten Fliehkräfte (phys. Zentrifugalkraft) nicht ausgeglichen sind. Für die Fliehkraft gilt:
Die Wirkung von Fliehkräften führt dazu, dass die gesamte Maschine zum Schwingen mit der Erregerfrequenz angeregt wird. Dadurch entstehen zusätzliche Belastungen für Lagerung und Fundamentierung. Die Erregerfrequenz entspricht dabei der Drehfrequenz der unwuchtbehafteten Welle. Die Schwingung hat harmonischen Charakter.
Eine statische Unwucht liegt vor, wenn der Schwerpunkt eines Rotors nicht durch seine Drehachse geschnitten wird. Dieser Rotor lässt sich durch Auspendeln auswuchten.
Jedoch auch ein statisch voll ausgewuchteter Rotor kann bei Rotation dynamische Kräfte erzeugen (Momentenunwucht). Insbesondere wenn es sich um langgestreckte Rotoren handelt oder der Ausgleichsebenenabstand größer als der Lagerabstand ist und die Schwerpunktachse nicht parallel zur Drehachse verläuft.
Das Vorhandensein einer Unwucht lässt sich durch Schwingungsdiagnose feststellen.
Verbesserung
Unter Verbesserung wird die Kombination aller technischen und administrativen Maßnahmen sowie Maßnahmen des Managements zur Steigerung der Funktionssicherheit einer Betrachtungseinheit, ohne die von ihr geforderte Funktion zu ändern, verstanden.
Teil der Instandhaltung
Verschleiß
Verschleiß ist der Vorgang des fortschreitenden Materialverlustes aus der Oberflächenschicht eines festen Körpers infolge Reibungskontakt mit einem anderen festen, flüssigen oder gasförmigen Körper oder Stoff. Man unterscheidet zwischen Gleitverschleiß und Rollverschleiß.
Gleitverschleiß
- Die Oberfläche wird plastisch verformt.
- Es bilden sich in Gleitrichtung Zungen aus.
- Zusätzlich findet spanabtragender Verschleiß statt, wobei mineralische Teilchen als Werkzeug dienen.
- Reibungswärme wirkt verschleißfördernd durch momentane Verschweißung und nachfolgende plastische Trennung.
- Die Ausbildung von plastisch verformten Zungen an Zahnflanken von Zahnrädern führt zu Auslösern für Ermüdungsschäden.
Rollverschleiß (an Wälzlagern)
- Der Ölfilm wird durchbrochen.
- Die innige mechanische Berührung führt zu starker Verformung und zu Gleitverschleiß. Der Gleitvorgang wird dadurch hervorgerufen, dass die Wälzkörper unter starker Belastung elastisch verformt werden und es somit zu Relativbewegungen zwischen den berührenden Oberflächen kommt.
Lokaler Verzahnungsschaden
Neben dem Zahnbruch konzentrieren sich insbesondere Zahnflankenermüdungserscheinungen, Deformationen und Dauerbruchanrisse auf einen oder wenige Zähne. Ist lediglich ein Zahn von n Zähnen geschädigt, so gestaltet sich der jeweils n-te Zahneingriff mit höherer oder aber verminderter Intensität. Für die Signalanalyse heißt das, dass die gleichmäßige Zahneingriffsschwingung einmal pro Umdrehung gestört wird. Das heißt, die Zahneingriffsschwingung wird mit der Drehbewegung des defekten Zahnrades amplitudenmoduliert. Dazu kommt, dass sich die Winkelgeschwindigkeit der Zahnräder geringfügig ändern kann, und es somit darüber hinaus zu einer Frequenzmodulation kommt.
Sind mehrere Zähne geschädigt, gilt analoges. Praktisch ist der lokale Charakter von Verzahnungsschäden gegeben, solange nicht alle Zähne geschädigt sind.
Verzahnungsschäden äußern sich im Spektrum des Signals. Man erkennt die durch den lokalen Verzahnungsschaden hervorgerufene Modulation als Seitenbänder zur Zahneingriffsfrequenz. Der Abstand des Seitenbandes zur Zahneingriffsfrequenz bezeichnet die Drehfrequenz des geschädigten Zahnrades. Es ist somit exakt zuzuordnen. Die Seitenbänder ihrerseits können Harmonische, also Vielfache, aufweisen.
Im Bild erkennt man verschiedene Seitenbänder, die tatsächlich zwei verschiedene Schäden bezeichnen.
Quelle der beiden Bilder: Wirth, R.: Maschinendiagnose an Industriegetrieben. Teil II: Signalidentifikation in der Praxis. Antriebstechnik 37(1998), Nr. 11, S.77-81
Verzahnungsschaden, umlaufender
Insbesondere Verschleißschäden an den Zahnflanken sind meist gleichmäßig auf alle Zahnflanken verteilt. Dem Wälzanteil der beiden im Eingriff befindlichen Zähne ist ein Gleitanteil überlagert. Der Gleitanteil nimmt mit der Entfernung des Eingriffspunktes (Berührungslinie der Zahnflanken im Schnitt) vom Wälzpunkt zu. Im Ergebnis abrasiver Voränge wird die Oberfläche der Evolvente daher ungleichmäßig verändert:
Die Abtragung der Evolvente oberhalb und unterhalb des Wälzkreises bewirkt eine Störung des Zahneingriffs. Die Zahneingriffsschwingung ist größtenteils ein Resultat der Elastizität der beteiligten Maschinenelemente (parametererregte Schwingung). Der ordnungsgemäße Zahneingriff liefert im Spektrum normalerweise nur den Zahneingriffspeak und in der Regel Harmonische mit abnehmender Amplitude.
Quelle der beiden Bilder: Wirth, R.: Maschinendiagnose an Industriegetrieben. Teil II: Signalidentifikation in der Praxis. Antriebstechnik 37(1998), Nr. 11, S.77-81
Im Spektrum äußert sich der umlaufende Verzahnungsschaden je nach Verzahnungsgeometrie durch das Ansteigen der Amplitude der Zahneingriffsfrequenz und der Ausbildung der Vielfachen zur Zahneingriffsfrequenz, den Harmonischen.
Vorbeugende Instandhaltung
Die vorbeugende Instandhaltung liefert nach fester oder flexibler Periode (auch periodische Instandhaltung) die Möglichkeit, Instandsetzungsmaßnahmen grundsätzlich zu Zeitpunkten durchzuführen, zu denen kein Anlagenbetrieb erfolgen muss.
Die Kosten dafür sind oft erheblich, da der Abnutzungsvorrat von Bauteilen in der Regel nicht verbraucht wird. Jedoch ist die vorbeugende Instandhaltung im Sinne der Sicherheit bei einigen Anwendungen zwingend notwendig.
Wälzkörperschäden
siehe WälzlagerschädenWälzkörperspinfrequenz
siehe WälzlagerkinematikWälzlagerkinematik
Aus der Wälzlagergeometrie leiten sich kinematische Frequenzen ab, deren Kenntnis zur Bestimmung der Art von Schädigungen an Wälzlagern notwendig ist. Dabei wird ideales Rollen vorausgesetzt. Das heißt, es findet kein Schlupf statt, der Einfluss der Massenträgheitskräfte ist vernachlässigbar und der Betriebsdruckwinkel ist für Innen- und Außenring gleich.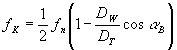
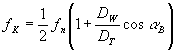
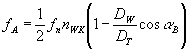
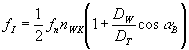
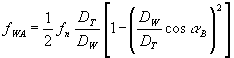
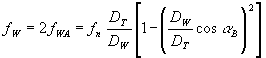
DT - Teilkreisdurchmesser
DW - Wälzkörperdurchmesser
a B - Betriebsdruckwinkel
fn - Drehfrequenz
z - Wälzkörper
Im Realfall kann ideales Rollen nicht zwangsläufig vorausgesetzt werden. Die Folge ist Schlupf des Wälzkörpersatzes, der - abhängig von Bauform und Einsatz des Lagers sowie Belastungsverhältnissen - beträchtliche Werte annehmen kann. Dies führt zur Abweichung zwischen mathematisch bestimmbarer und tatsächlicher kinematischer Frequenz. In der Praxis hat es sich bewährt, eine geringfügige Abweichung der kinematischen Frequenzen durch Festlegung einer Toleranzgrenze zuzulassen. Somit wird zumindest geringfügiger Schlupf kompensiert.
Wälzlagerschäden
Wälzlagerschäden können
- Wälzlagerlaufbahnschäden oder
- Käfigschäden
sein. In jedem Fall führen sie zu periodischen Stoßimpulsfolgen. Zur Visualisierung der Stoßimpulsfolgen eignet sich das Hüllkurvenspektrum.
Die Wälzlagerlaufbahnschäden müssen aus diagnostischer Sicht wiederum unterschieden werden in
- bezüglich der Lastzone nicht umlaufende Schäden (lokale Wälzlagerschäden) und
- bezüglich der Lastzone umlaufende Schäden (umlaufende lokale Wälzlagerschäden).
Für den einfachsten Fall einer Wälzlageranordnung mit feststehendem Außenring und konstanter Lastrichtung, beispielsweise in Richtung der Gewichtskraft, heißt das, dass
- der Außenringschaden ein lokaler Wälzlagerschaden,
- der Innenringschaden ein umlaufender lokaler Wälzlagerschaden und
- der Wälzkörperschaden ebenfalls ein umlaufender lokaler Wälzlagerschaden
sind.
Wälzlagerschaden
siehe Umlaufender lokaler WälzlagerschadenWartung
Unter Wartung versteht man die Maßnahmen zur Verzögerung des Abbaus des vorhandenen Abnutzungsvorrats.
Wellenanriss
Die vier Phänomene lose Teile, lose Verbindungen, Passungsrost und Wellenanriss werden hier, obgleich die Ursache sehr verschieden sein kann, zusammen betrachtet, da sie aus diagnostischer Sicht zunächst nicht trennbar sind.
Fremdkörper, die sich um die Welle gewickelt haben, oder aber Teile an der Welle, die sich gelöst haben, können einmal pro Umdrehung an Statorteile anschlagen. Ähnliches geschieht, wenn Fremdkörper in den Aktionsbereich rotierender Teile hinein geführt werden. In diesen Fällen treten Stöße zwischen sich drehenden und ruhenden Komponenten auf.
Der gleiche Effekt tritt auf,
- wenn Bauteile, die auf der Welle fehlerhaft montiert sind und arbeiten,
- bei Passungsrost zwischen auf der Welle montierten Teilen und der Welle,
- wenn die Welle angerissen ist und ihre Biegesteifigkeit folglich über den Azimut variiert oder
- wenn fehlerhaft montierte Wälzlager in ihrem Sitz arbeiten.
Vorausgesetzt, die Welle unterliegt einer radialen Belastung, wird sich durch die Rotation der Welle einmal pro Umdrehung ein - wenn auch kleiner - Spalt auftun und wieder schließen. Entsprechend der Drehfrequenz wird sich dieser Vorgang mehrmals pro Sekunde wiederholen, was zu Aufprallgeschwindigkeiten führt, die einem Stoßimpuls entsprechen. Und genauso ist die Wirkung auf die umgebende Maschine. Wir detektierten eine Stoßimpulsfolge mit der Drehfrequenz.
Stoßimpulsfolgen können wir im Hüllkurvenspektrum sichtbar machen.
Im Hüllkurvenspektrum erkennt man deutlich, dass der Drehfrequenzpeak im enormer Intensität auftritt. Ursache war - wie nach der Demontage eindeutig klar wurde - ein Wellenschaden im Bereich der Passfeder.
Quelle der beiden Bilder: Wirth, R.: Maschinendiagnose an Industriegetrieben. Teil II: Signalidentifikation in der Praxis. Antriebstechnik 37(1998), Nr. 11, S.77-81
Wellenschwingungsanalyse
Wellen- und Verzahnungsschäden führen zu einer der durch den Schaden erzeugten Kräfte konformen Oszillation der Welle. Auch Stöße, die aus Wälzlagerschäden resultieren, wirken gleichermaßen auf das Gehäuse und die Welle. Daher liegt nahe, dass man durch Unregelmäßigkeiten erzeugten Schwingungen auf der Welle erfassen kann.
Erfasst wird die Wellenschwingung. Dies wird mittels Wirbelstrom-, induktiver oder optischer Sensoren realisiert. Erfasst wird die Wellenschwingung in zwei radialen sowie in axialer Richtung. Voraussetzung ist natürlich, dass die Welle eine für die Messung hinreichend glatte Oberfläche besitzt, damit Wegaufnehmer hoher Empfindlichkeit eingesetzt werden können. Hundertprozentiger Rundlauf ist dagegen nicht zwangsläufig nötig.
Im Spektrum dominiert natürlich der Drehfrequenzpeak. Um andere Peaks deutlich zu erkennen, empfliehlt sich das Herausvergrößern des interessierenden Bereichs - hier 80 .. 140 Hz. Im Bild erkennt man anschaulich, dass der Innenringpeak mit Seitenbändern abgebildet wird.
White Etching Crack
Ein bislang weniger bekannter Schädigungsmechanismus ist das White Etching Crack (WEC) (auch White Etching Area, White Structure Flaking oder Brittle Flaking). Charakteristisch ist eine weißanätzende Strukturveränderung, eine Entkarbonisierung unterhalb der Laufbahnen von Wälzlagern. Momentan gibt es eine Reihe von Forschungsvorhaben zu dem Thema. Formal muss es vermutlich in die Rubrik Alterung eingeordnet werden.Zahneingriffsfrequenz
siehe GetriebekinematikZahneingriffsschwingung
Aus diagnostischer Sicht wird unter Zahneingriffsschwingung die Grundschwingung verstanden, die dadurch entsteht, dass zwei Zahnräder ineinander greifen und die Flanken der einzelnen Zähne so aufeinander abrollen bzw. aufeinander gleiten.
Die Zahneingriffsfrequenz berechnet sich aus der Getriebekinematik und entspricht dem Produkt von Drehfrequenz und Zähnezahl desselben Zahnrades.
Die Nachweisbarkeit der Zahneingriffsschwingung im Spektrum des Schwingungssignals eines Getriebes ist normalerweise kein Hinweis auf Unregelmäßigkeiten. Treten jedoch Harmonische (Vielfache) zur Zahneingriffsschwingung auf oder kann man die Zahneingriffsschwingung im hochpassgefilterten Hüllkurvenspektrum nachweisen, so kann auf eine umlaufende, also alle Zähne betreffende Zahneingriffsanomalie geschlussfolgert werden. Schäden an nur einem oder mehreren Zähnen führen infolge der Amplitudenmodulation zu Seitenbändern zur Zahneingriffsschwingung im Abstand der Drehfrequenz des geschädigten Zahnrades.
Nicht gemeint ist hier die Zahnschwingung, die durch die auf die Zähne im Eingriff wirkende Kraft verursacht wird und zur elastischen Durchbiegung oder Verwindung der Zähne führt.